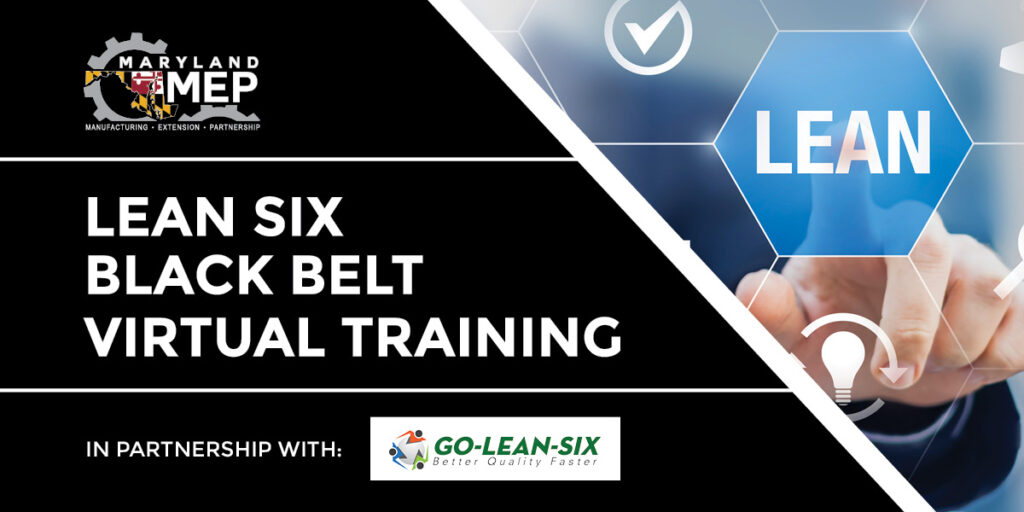
Lean Six Black Belt Virtual Training
Investing in our employees as we drive continuous improvement throughout our organization remains foundational. The capability to identify, organize and lead projects as well as drive out waste in our manufacturing and office processes is fundamental to growth, efficiency, safety and quality. This professional development training will provide the necessary skills and tools for us to continue to thrive even during challenging times.
This 15-day training will be presented in a live virtual workshop format; hands-on with real-life simulations and examples. Each participant will be required to complete a Lean Six class project that provides immediate application and results! These projects typically return 5 to 20 times the training investment in less than one year.
Intended Audience:
- Executives, Managers, Supervisors, Engineers, Lean-Six OpX Practitioners & CI Facilitators
- A minimum of 5 participants are required in order to begin the training.
Training / Session Outline:
- 09/05/25 – Introduction to Lean Principles, Strategies & Techniques (8 Wastes)
- 09/12/25 – Kaizen Events (Plan, Conduct & Follow Up)
- 09/19/25 – 6S Workplace Organization Kaizen
- 09/26/25 – Lean Daily Management (SQDC)
- 10/03/25 – Root Cause & Corrective Action (8D)
- 10/10/25 – Six Sigma – DMAIC (Define, Measure, Analyze, Improve, Control)
- 10/17/25 – Kanban Pull Systems (PFEP)
- 10/24/25 – Continuous Flow (Cellular Layouts)
- 10/31/25 – Quick Changeover (SMED)
- 11/07/25 – Total Preventive Maintenance (TPM)
- 11/14/25 – Lean Leader / Facilitator / Coach (LFC)
- 11/21/25 – The Eight Steps of Value Stream Management (VSM)
- 12/05/25 – Six Sigma – Statistical Process Control (SPC)
- 12/12/25 – Creating a Continuous Improvement Culture (Kata)
- 12/19/25 – Lean-Six Transformation / Leading the Lean-Six Journey
Why Go-Lean-Six Belt Certificate Boot Camp?
- Our workshops are designed from years of successful operations and business experience and are built on the Toyota Production System Model for a firm foundation.
- These fifteen workshops build on each other, from introduction (Yellow Belt) to more advanced methods and topics (Green Belt & Black Belt) relevant to: Executives, Managers, Supervisors, Engineers, Lean-Six OpX Practitioners & CI Facilitators
- The Bootcamp is applicable to a wide variety of businesses including healthcare, engineering, manufacturing and other industries.
- Virtual training often provides a forum to focus on the learning experience, benchmark other companies, and share lessons learned.
- Workshops are interactive and include simulations, projects with hands-on demonstrations. They are designed to be immediately applicable to your needs.
- Go-Lean-Six Consulting LLC is local and experienced. Follow on support is available.
Program Details
DATE & TIME:
- Begins on September 5, 2025 and will run for 15 consecutive weeks
- This training will be held virtually from 8:30 am-4:30 pm
LOCATION:
- Virtual
COST:
- $3,900 – Maryland Manufacturers
- $4,900 – Non-Manufacturers
- The EARN Maryland Program may fund a portion of the training cost for manufacturers.
For more information please contact:
Sara Keith
Please contact Sara Keith for information regarding the next Lean Six Black Belt Training.
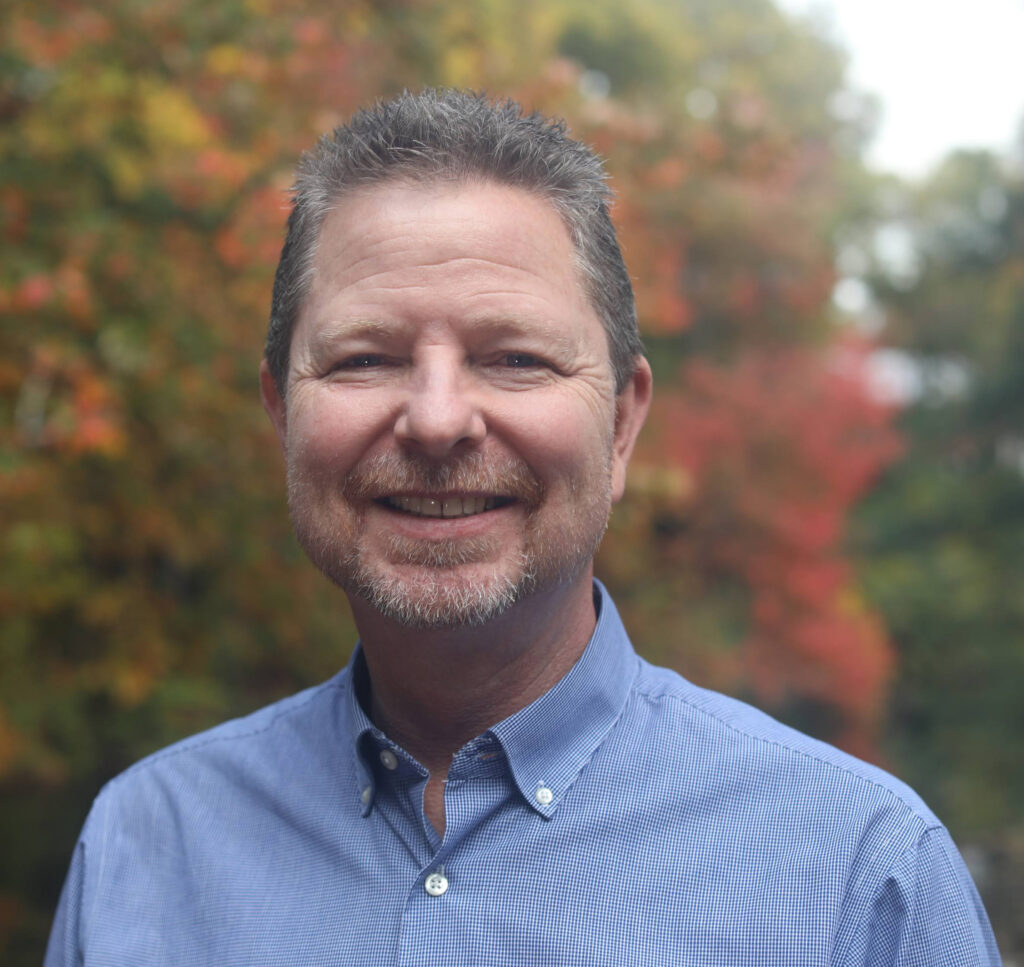
About the Instructor:
Dan Roth
President, Go-Lean-Six Consulting
Dan Roth is President of Go-Lean-Six Consulting LLC, a Lean Six Sigma consulting and training firm. Dan is a Lean Six Sigma Master Black Belt that provides strategic leadership and “on site” mentoring for the Go-Lean-Six Consulting team. Dan started as a Go-Lean-Six Consultant and progressed to a Lean-Six Black Belt, Director of Operational Excellence, Lean-Six Master Blackbelt and now the President / CEO of Go-Lean-Six Consulting. Dan brings over 20 years’ experience in manufacturing and 22+ years’ experience in leadership, teaching, training, coaching, and mentoring to his training and consulting.
Dan has pioneered hands on workshops that not only train learners but help them apply and sustain those Lean tools and methods to daily work activities. He has been a key part of the Go-Lean-Six transformation to include onsite and virtual services in response to COVID-19 as the team continues to support clients throughout these new challenging times.
Dan has helped a variety of industries improve their processes using Lean Six Sigma including Defense, Healthcare, Pharma/Medical, Aerospace, Garment, Cosmetics, Food and Beverage, Machine manufacturing, Silicon chip / Semiconductor, Plastics, Transportation, and a verity of other industries.
Maryland manufacturers
Maryland MEP Incumbent Worker Training Program
Maryland MEP through the Maryland Department of Labor’s EARN initiative has made funding available for Maryland manufacturers to assist with the total cost of training for incumbent workers. To be eligible, your organization must be registered with Dun and Bradstreet and have a valid manufacturing NAICS code, and have a physical location in Maryland.
Eligible Maryland manufacturers qualify to have $1,000 funded through the Maryland Department of Labor’s EARN Maryland Program.